Revealing the Core Technical Differences of Two Aramid Separators and How They Enhance Battery Safety and Cycle Life
I. The Importance and Market Trends of Separator Materials
The separator, a core component of lithium batteries, plays a crucial role in isolating electrodes and conducting ions. With the surge in demand for new energy vehicles and energy storage, the global lithium battery separator market is expected to exceed 3.7 billion yuan by 2025. Aramid-based materials, known for their high-temperature resistance and anti-puncture properties, have become a focal point for technological upgrades.
II. Aramid-Coated Separator: Technical Characteristics and Advantages
Definition: A layer of aramid polymer is coated on the surface of a polyolefin (PE/PP) base film, forming a dual-layer porous structure (with a pore rate of 35%-45% in the base material and a dense network in the aramid layer).
Core Performance:
- High-Temperature Resistance: With a heat resistance of up to 400℃ and a thermal shrinkage rate of less than 5% at 180℃ (compared to traditional ceramic separators that shrink at 170℃).
- Anti-Puncture Strength: Puncture strength of ≥600g (compared to 435g for ceramic separators).
- Electrolyte Wettability: Polar molecular structure improves liquid absorption by 30% and reduces internal resistance by 15%.
- Safety: The aramid layer remains intact after the base material melts, reducing the risk of thermal runaway by 70%.
Application Scenarios:
- Power batteries (for high-temperature resistance): New energy vehicles, energy storage systems.
- High-rate batteries: 5G base stations, drone power sources (optimized for fast charging performance).
III. Aramid-Based Separator: Technical Characteristics and Advantages
Definition: Made directly from aramid fibers, the separator is chemically treated to form an all-aramid microporous membrane (without a polyolefin layer).
Core Performance:
- High-Temperature Stability: Thermal decomposition temperature >400℃, with a long-term operating temperature of up to 280℃.
- Oxidation Resistance: Molecular chain hydrogen bonding resists electrolyte corrosion, enhancing cycle life by 50%.
- Mechanical Strength: Tensile strength of ≥120MPa, with better tear resistance than coated types.
- Lightweight: Density of 1.44g/cm³, reducing weight by 35% compared to traditional separators.
Application Scenarios:
- Solid-state/battery: Compatible with high-voltage electrolytes for increased energy density.
- Military/aerospace: High reliability required in extreme environments.
IV. Performance Comparison and Selection Decision
Technical Parameter Comparison Table
Index | Aramid-Coated Separator | Aramid-Based Separator |
---|---|---|
Base Material Structure | PE/PP + aramid coating | Pure aramid fiber base material |
Thickness (μm) | 9-16±1 | 10-15±1 |
Air Permeability (s/100cc) | 200-240 | 150-180 |
Puncture Strength (g) | ≥600 | ≥800 |
Thermal Shrinkage at 180℃ | ≤5% | ≤3% |
Cost (yuan/m²) | 2-3 (scalable) | 4-5 (high technical barriers) |
Data source: Blue Course/ Guojin Securities Research |
Selection Suggestions:
- Prioritize Coated Type: For cost-sensitive scenarios (consumer electronics, energy storage), balancing performance and budget.
- Prioritize Base Type: For high-end power batteries/military fields, pursuing extreme safety and life.
V. Industry Cases and Commercial Conversion
- Taihe New Materials: With a global aramid production capacity of 23,000 tons, the cost of coated separators is only 1 yuan/m² higher than ceramic types, and has been supplying Huawei and State Grid.
- Breakthrough in Solid-State Batteries: Aramid-based separators enable high-speed lithium-ion transport, improving cycle stability by 40%.
Customization Service Module
- Parameter Customization: Base material porosity (30%-50%), coating thickness (1-5μm)
- Composite Process: Aramid + nano Al₂O₃ doping (thermal stability improved by another 20%)
- Certification Support
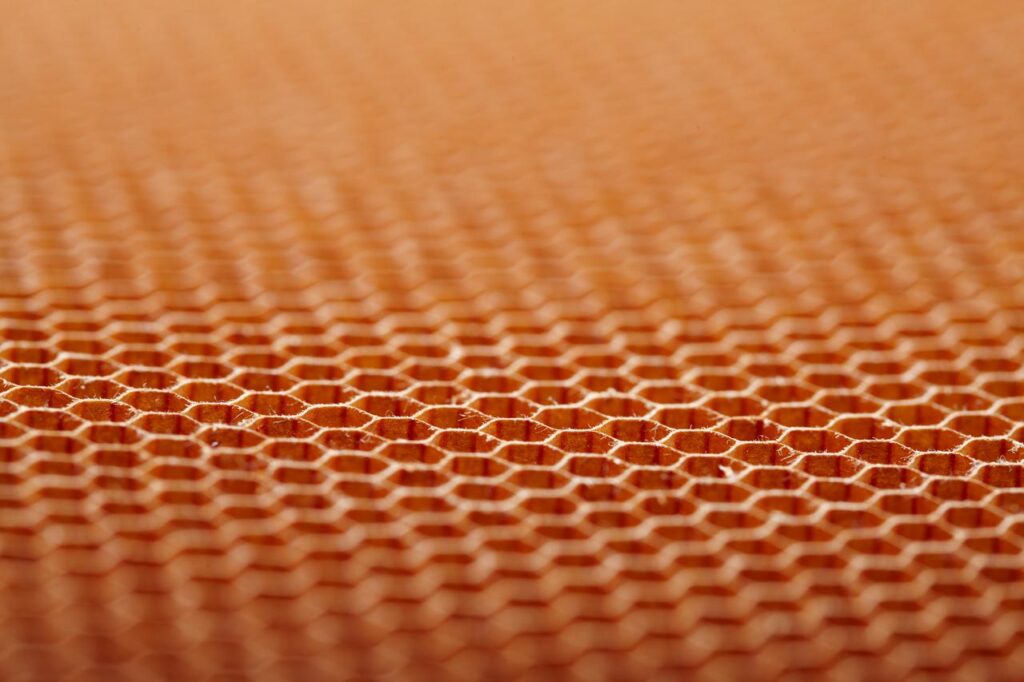